THE FURNACE CONDUCTORS GUARDIANS OF FIRE
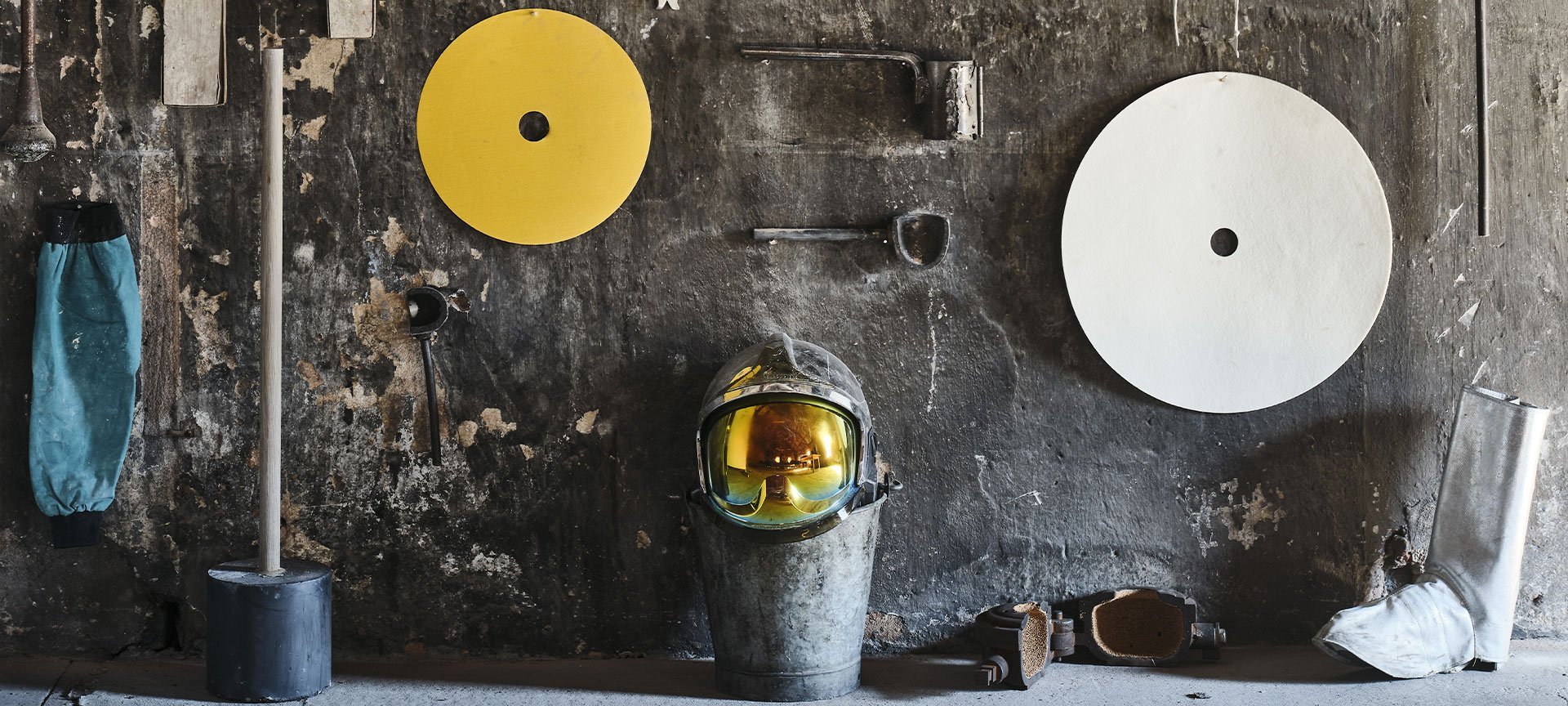

After suiting up with their aluminum suits, booties, helmets, and gloves, the furnace conductors, normally addressed as ‘tiseurs’ in French, can finally tread toward the pot furnace. Their visors, needed to examine the erupting magma, are identical to those used to observe solar eclipses. Just 5 meters from the epicenter of the crystal magma, the heat has already reached 900 degrees Celsius. As they get closer, the air gets thinner. Wearing 10 kg of body armor, reminiscent of the Apollo astronauts on their missions, every gesture requires an exceptional effort.
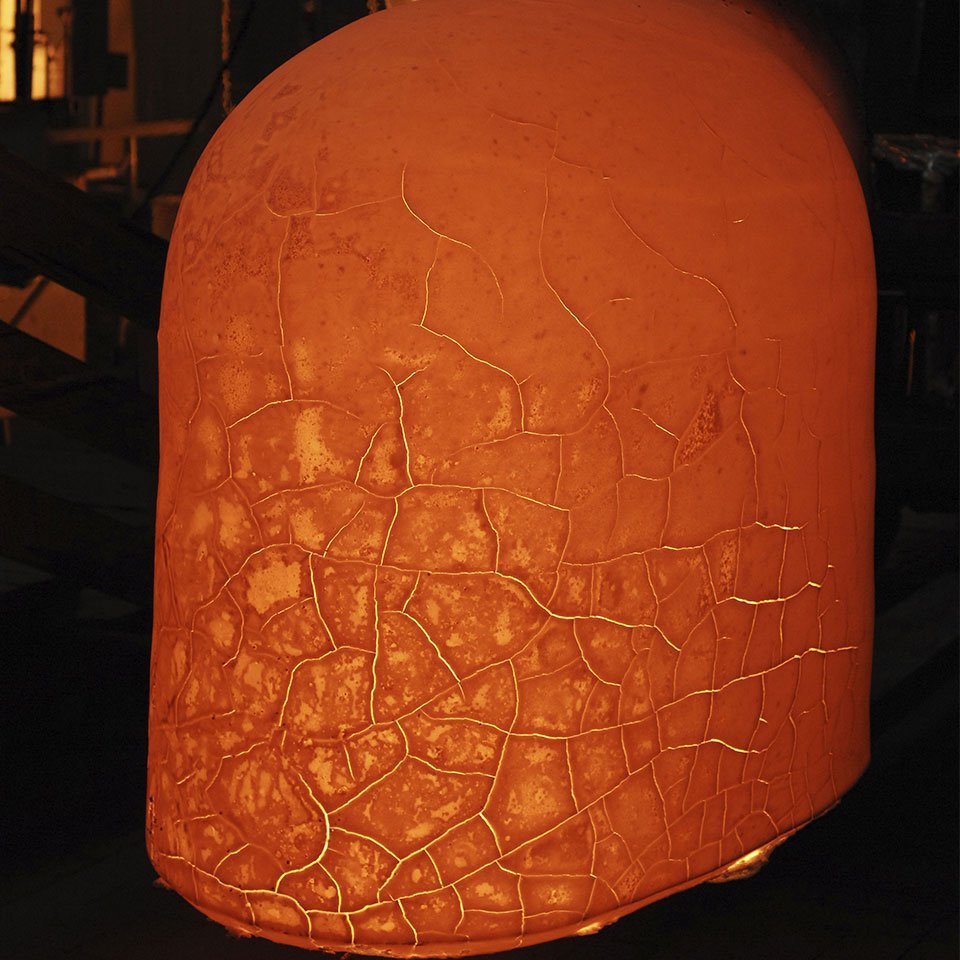
At the manufacture, seven tiseurs keep their eyes on the fire. There is not only one but two furnaces in the hot workshop where they maneuver around. The first, the tank furnace, is dedicated to make 10 tons of clear crystal. Meanwhile, the pot furnace holds 3.5 tons of colored crystal in its 9 containers, each successively holding one of Saint-Louis's 17 color tints. Changing these refractory earthenware pots is the most technical and spectacular operation in the tiseur's craft; a critical technique to prevent impurities from cracking clay.
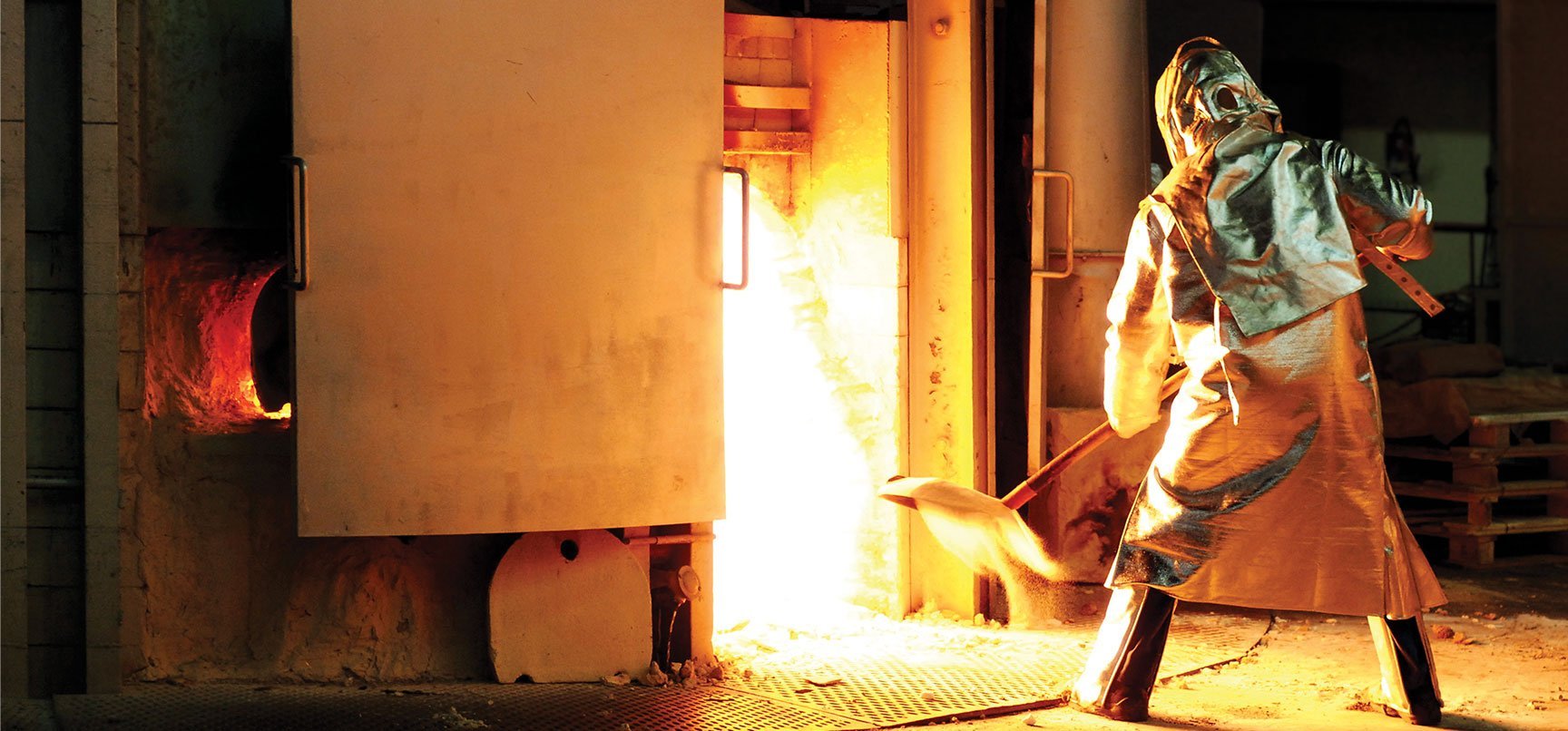
Still handmade by Saint-Louis potters and dried for months, the clay pot ensures optimum fusion and perfect crystal color. But after a few months of use, the worn-out vessel needs to be replaced by a team of 4 or 5 tiseurs. The pot weighing several hundred kilos is extracted by hand, while it is still glowing and almost ablaze.
The pot filled with molten crystal is shattered on the floor, where it slowly cools down. A new pot, heated up to 1,200 degrees Celsius, is extracted from a nearby furnace called a ‘carcaise’. Then it is gently slid into the furnace to prevent any thermal shock. The whole act must be done seamlessly, from inserting the pot to closing the door.
The operation concludes when the crystal craftsman picks up the molten crystal with his pipe from the ‘scooping’ bay of the pot. The tiseur tolerates the heat that tingles his skin and stings his nose. The smell of clay and heated aluminum wafts through the hall. His eyes sparkle when an orange ball wiggles under his nose. Finally, it is time for a break.
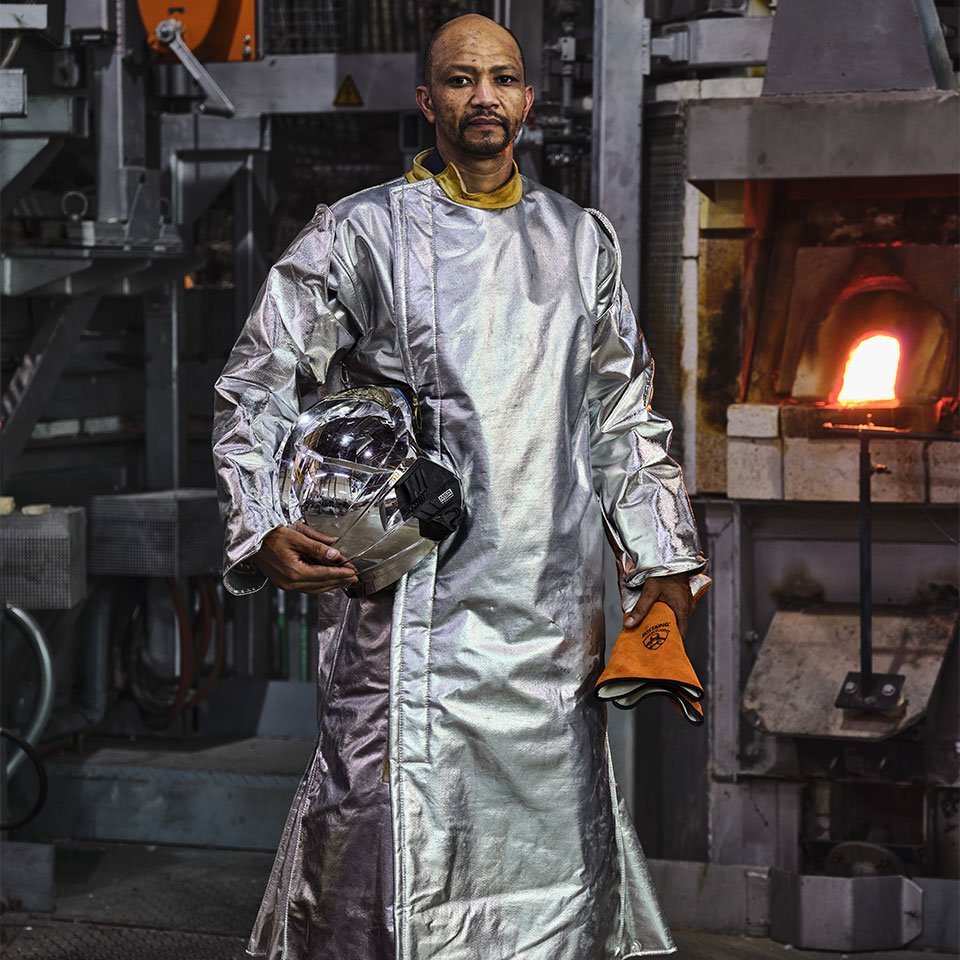
The interview
“In the past, furnaces were fueled with firewood straight from the Vosges forest. You had to keep turning the embers, which translates as ‘tison’ in French, to keep the fire going, and hence how the French word ‘tiseur’ originated,” Julien Portaz, team leader who is responsible for the melting and fusion process, explains. “It's a great responsibility, both materially and symbolically.”
Since 1586, the manufacture has taken care of the fire
in a precise manner. A drop in electricity or gas supplies would jeopardize crystal quality even nowadays. The large melting furnace also needs to be renewed every six years.
The fire has to be extinguished completely and then relit. The operation takes two months. The roar stops, and the heat recedes. “It's a strange and uncomfortable period for everyone,” Julien Portaz attests. “But when the rumbling of fusion and the intense heat return, we are back in the game!”.
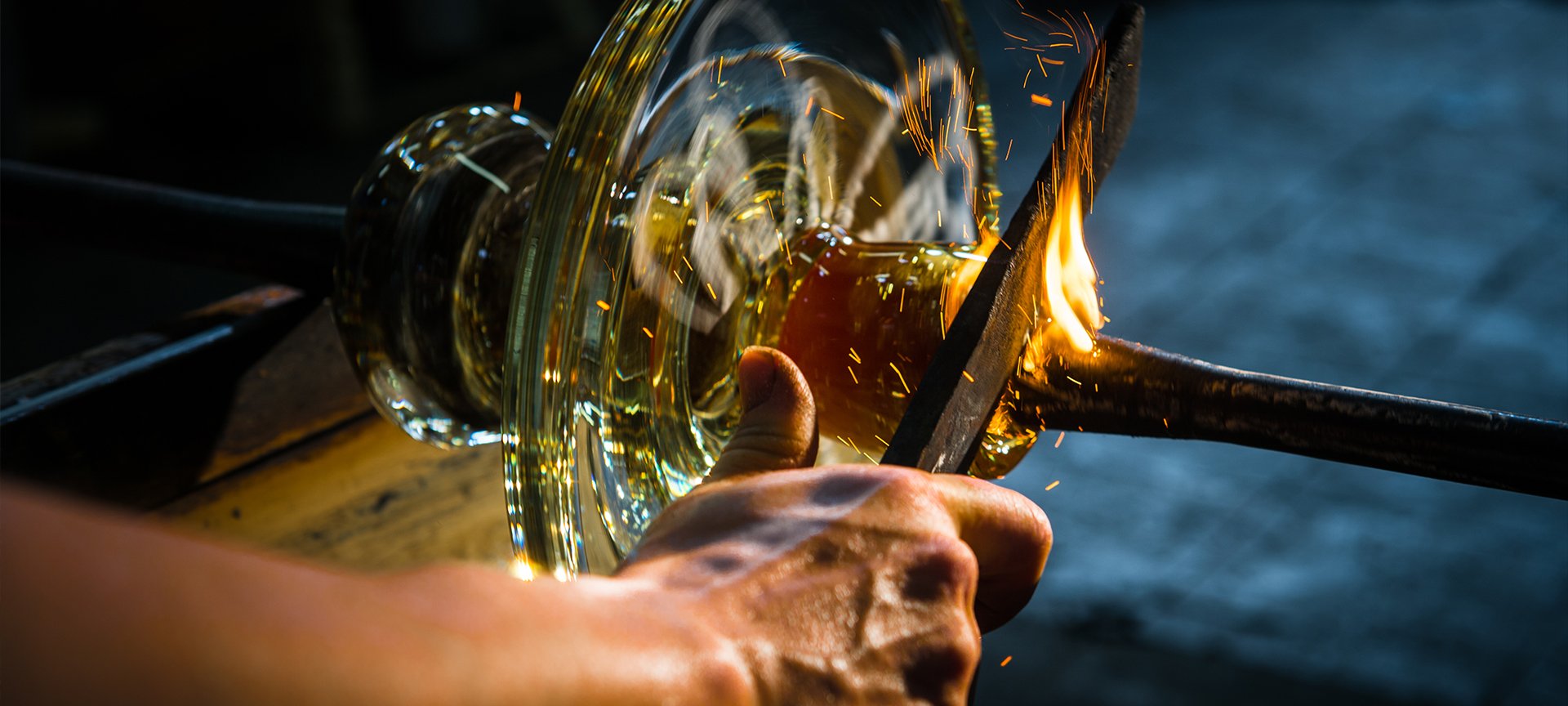
Know-howSaint-Louis
DISCOVER MORE